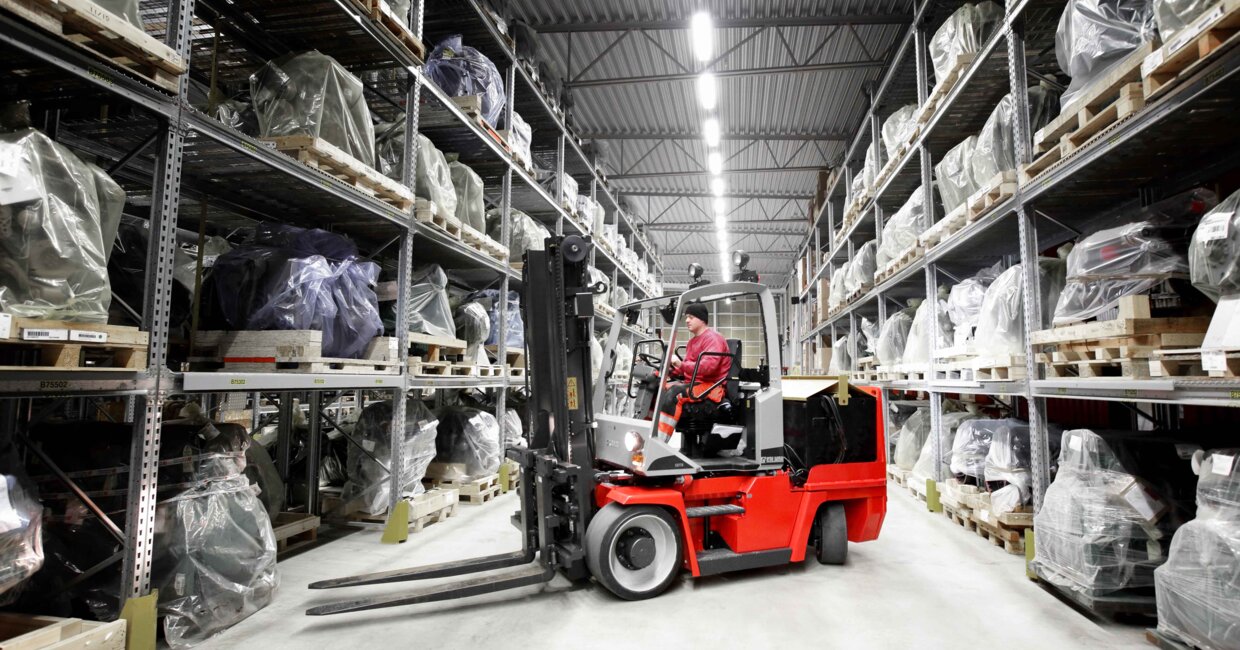
Lifting safety to new levels
National Forklift Safety Day is a timely reminder of the human - and commercial - value of safer forklift truck operations.
Data from the US Bureau of Labor Statistics highlights the risks associated with operating forklift trucks. Between 2011 and 2017, 614 workers lost their lives in forklift-related incidents and more than 7000 non-fatal injuries were recorded each year.
Established in the US in 2013 by the Industrial Truck Association (ITA), National Forklift Safety Day is a global initiative aimed at raising awareness of safe use of forklifts and the importance of proper operator training. This year the focus of the event, to be held on June 8th, is safe maintenance practices and the importance of thorough examinations and pre-shift inspections.
A proactive approach
“With more than one in ten of the estimated 855,000 forklift trucks in operation across the US involved in an accident every year, the importance of this event is self-evident,” observes Jason Murnane, Vice President, Solution Sales Counterbalanced Equipment, Kalmar.
“We spend a lot of time educating the market about the safety features and options available on our equipment because some customers are not fully aware of the options,” he says. “Our approach is to promote safety features the customer may not have even considered.”
Murnane acknowledges that larger companies are more likely to include safety as part of the tender process. “These companies typically have a safety manager who would give input in the purchasing decision, whereas in small organizations the operations manager or purchasing manager will have sole responsibility for procurement.”
This reinforces the value of events like National Forklift Safety Day. “It is about getting out in front of unsafe practices because when we receive a request for a safety option, it usually comes after the customer has had an accident,” Murnane explains. “We are taking a proactive approach to increase awareness of features that could prevent an accident from happening in the first place.”
“We are taking a proactive approach to increase awareness of features that could prevent an accident from happening in the first place.”
Tony Kordes, Project & Product Manager, Kalmar USA, says that promoting safety as a means of reducing product and facility damage, as well as injury to operators and other employees, is a powerful message.
“A company that invests in a rear view camera for its forklifts to reduce damage to product or facilities, for example, may find that it is also making the workplace safer for its employees. In terms of specific features we are seeing increased demand for speed limiters. We offer additional options to slow trucks down based on whether they have a raised load or are loaded, allowing the machine to run slower in specific circumstances rather than all the time.”
Murnane notes that many of the safety features on Kalmar forklifts are standard features. “For example, our standard cabin has no front corner posts and we don’t put the exhaust in the middle of the rear window,” he says. “All of these design features add to the production cost.”
Focus on safety each and every day
Kalmar reachstackers also come with built-in overload protection, so the operator cannot raise the boom or go any further out if they are over a certain load, and seatbelt interlock options can help enforce Occupational Safety and Health Administration (OSHA) requirements. Other important safety options include a 180 degree rotating seat and the Blaxtair rear camera system.
“Our focus is on doing everything in a safe and secure environment.”
The Blaxtair camera is a pedestrian detection aid that uses algorithms to analyse the rear camera image, determine if there is a pedestrian in view and if they are in a danger zone, and present this information on a display in the cab.
“The rotating seat is important for improving visibility on long rearward drives,” says Kordes. “In the US, operators are prohibited from driving with a raised load, so if they have a tall load they cannot see over, they have to drive in reverse. As a result, US forklifts are driven backwards a high percentage of time, so with a rotating seat the operator doesn’t have to twist around, which helps to reduce back strain as well as improve visibility.”
Murnane describes safety as an ongoing conversation at every point of contact. “Our focus is on doing everything in a safe and secure environment,” he concludes. “Safety needs to be a focus every day of the year.”
Related articles
Subscribe and receive updates in your email
Subscribe