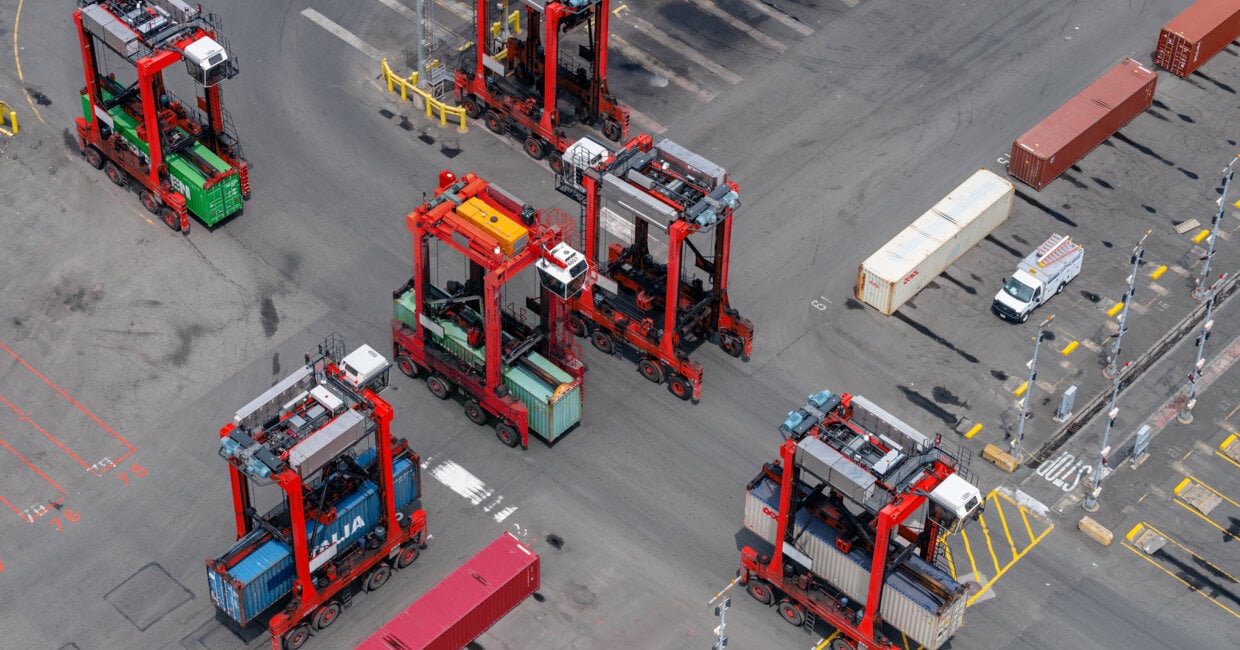
Collision warning system improves safety of manual straddle carriers
Safety is a key concern for terminal operators, and one of the key areas to address is applications in which heavy container handling equipment must operate in areas with mixed traffic or people. Equipment or cargo damage can lead to costly delays and disrupt operations.
The manually operated straddle carrier is an ubiquitous type of container handling equipment at terminals around the world, but until recently, this classic type of machine has seen little in the way of advanced safety-improving solutions and driver assisting technology.
Kalmar is now introducing a collision warning system for its manually operated straddle carriers. The system is available as an optional add-on for new machines and as an upgrade for existing machines. It increases safety by providing the driver with visible and audible warnings when there is a risk of collision, giving them more time to react to potential hazards. In addition to detecting obstacles in the machine’s path or blind spots, the system also warns the driver if the spreader (whether empty or laden) is too low when the machine is approaching a container stack. The driver remains in full control of the machine at all times.
"Collisions in your yard can cost your business time, money and have a negative impact on your operations and safety levels," says Timo Alho, Director, Product Management, Kalmar. "Our new collision warning system helps prevent and reduce the severity of collisions, allowing your equipment to operate more efficiently and safely with minimal downtime," he adds.
"Collisions in your yard can cost your business time, money and have a negative impact on your operations and safety levels."
Active safety
Kalmar's collision warning system is a robust solution for area surveillance and active obstacle detection. The system uses multiple sensors fitted to the straddle carrier to survey the surrounding area and actively warn the driver of obstacles in the path of the machine, its spreader or the container being carried. This allows the driver to take immediate evasive action to reduce the risks of collision and damage to equipment or containers, saving time, money and extending the life of the straddle carrier fleet.
The system has a high ingress protection rating, shock and vibration resistance as well as a wide operating temperature range. The collision warning system includes multiple overlapping functions for warning the driver of obstacles on the path of the machine; if the spreader and container are too low when going towards the container stack; or if a collision is imminent with an object in the blind spot at the side of the straddle carrier.
Forward sensing in both directions of driving is provided by a combination of sensors on the topframe and sideframe corners of the vehicle. The topframe sensors monitor the areas in both driving directions from the lowest to highest container tiers. Sideframe corner sensors monitor the drive path of the vehicle and provide object detection information to the driver's display in the cabin. The system tracks objects picked up by the sensors and provides time-to-collision and obstacle criticality information on the display.
Multilevel sensoring
The collision warning system provides the driver with a simple, easy-to-read graphic user interface (GUI) that indicates the direction and criticality of a potential collision. Additionally, a live view function is available with real-time camera views from all the sensors on the machine.
When driving into and out of the container stack, the system receives velocity, yaw rate and direction information from the machine control system. This information is used to project the vehicle wheelpath, so obstacles are monitored only on the path in order to minimise false detections when driving into the stack. The system provides the operator with visual indicators (green, yellow and red) in the GUI, as well as audible warnings when yellow or red warnings are active.
While in the stack, the system monitors obstacles in front of the sideframes of the moving machine, so objects within the cargo space of the straddle carrier will not cause an alarm. The system also monitors for other straddle carriers in the stack, so if the top frame cameras detect an object in the front within the specified warning area, an audible warning is activated.
The system also provides obstacle detection between the spreader and stack, the container load to the stack, as well as obstacles further on the horizon. Spreader height and load status information provided by the machine control system is used to determine the appropriate detection range for each situation. An alarm is activated if obstacles are identified within the detection range.
Smart safety
When driving on the apron or in other open areas, the system actively monitors for obstacles on the projected wheel path of the straddle carrier. Vehicle speed information is used to extend the detection range when needed.
The front and rear sensoring along the driving directions of the vehicle is supplemented by blind spot sensors that monitor two progressively closer zones on the left side of the straddle carrier. Monitoring of the blind area is activated whenever the driver steers more than a set threshold towards the side of the blind spot. Visual alarms are always active when objects are detected inside these zones, and audible warnings are sounded if the driver continues to steer towards the obstacle in the blind spot.
In addition to sensing obstacles at ground level and in the container stack, the collision warning system monitors the area above the container yard up to the level of the topframe of the straddle carrier. When driving out from the container stack, the system can detect another straddle carrier approaching from the side when it enters the detection area of the sensor system, providing the driver with a visual alarm on the GUI.
Depending on environmental conditions, the maximum obstacle sensing range of the system is typically in the range of 20–50 m. System functions may be limited due to severe weather conditions, such as heavy rain, snow, or fog. Direct sunlight also may affect the range of detection.
Multiple benefits
"The primary advantage of having a collision warning system on straddle carriers is of course increased safety," notes Timo Alho from Kalmar. "By providing timely alerts to the driver about potential collisions, the system can significantly reduce the occurrence of collisions by warning the driver about obstacles. However, the solution can also decrease the maintenance requirements on the machine, increase overall availability and extend its lifetime due to fewer collisions. Insurance companies recognize the safety benefits of such systems, so having a collision warning system installed on a straddle carrier may result in savings on insurance premiums."
"The primary advantage of having a collision warning system on straddle carriers is of course increased safety."
The new collision warning system is currently available for the full range of Kalmar straddle carriers, including the company's diesel-electric, hybrid and electric straddle carriers. Straddle carriers from other manufacturers may be compatible depending on the specific data inputs of the machine control system, as well as the possibility for finding suitable installation locations for the required sensors.
Related articles
Further reading
Subscribe and receive updates in your email
Subscribe